Definitive Feasibility Study
The development of the Windimurra project has been systematically studied since AVPL acquired the project in 2016. This work culminated in the completion of a DFS.
The DFS confirmed the robust technical and economic feasibility of the project.
The study was undertaken on the basis of the existing mineral resources, which only cover 6 kilometres of the known 27 kilometre magnetic anomaly at Windimurra and delivered an initial mine life of 31 years.
The DFS shows the project development will require A$213 million capital expenditure and produce approximately 7,600 tonnes per annum of high purity vanadium pentoxide flake (V2O5).
Key outcomes of the study are summarised in the table below.
DFS Highlights - Steady State Average1
|
Life of mine
|
31 years
|
Strip ratio
|
1:1
|
Annual mill throughput
|
2.8 million tonnes
|
Average annual production
|
7,608 tonnes V2O5
|
Total capital expenditure
|
A$213 million
|
1 Based on AVPL financial model and certain assumptions
Mine Design
Mining at Windimurra involves simple open cut mining undertaken using traditional load and haul equipment operating on day shift only. An extremely low life of mine (LOM) strip ratio of 1 tonne of waste per 1 tonne of ore is achieved by the robust and flexible design of the crushing, milling and beneficiation (CMB) circuit which enables effective processing of both the massive magnetite lenses and the disseminated magnetite hosted in fresh and weathered gabbro material.
The LOM ore reserve of 87.5 million tonnes includes no inferred mineral resource.
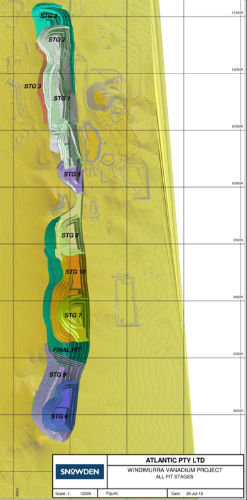
Metallurgical Test Work and Process Design
Preliminary metallurgical test work programs were undertaken on existing ROM stockpile material and costean samples taken from the existing pit floor. This program developed a new understanding of the drivers of magnetic recovery and concentrate grade from the various ore types. These new recovery and concentrate grade drivers enabled the development of new metallurgical algorithms for the deposit.
The DFS focused on further developing these metallurgical algorithms using composite samples derived from PQ diamond drill holes undertaken over a 5 kilometre strike length of the ore body. A total of 21 spatial variability composite samples consisting of a mixture of oxide, transitional and fresh ore along with two master composite samples (oxidised and fresh ore) were constructed from the diamond drill core resulting in a total sample mass of 3,770 kilogrammes.
In addition, a total of 29 separate sections of whole core were provided for physical and comminution test work.
The samples underwent a range of grinding and magnetic separation tests to develop the optimum process plant flow sheet design. This design was tested against all the variability composite samples to ensure its suitability for all ore sources.
Mineralogical analysis of the products indicated that fresh ore recovery is exceptional with only low intensity magnetic separation (LIMS) required. The more oxidised materials require the application of medium intensity magnetic separation (MIMS) to ensure suitable recovery of weathered magnetic particles.
Application of regrind to produce a concentrate of P80 90 um was found to consistently produce a final concentrate with <2.5% SiO2, a key outcome required to achieve high salt roast recoveries in the roasting process. Test work undertaken on magnetic concentrates produced from both fresh and oxidised ores yielded similar V2O5 recovery performance with conversions ranging from 84% to 92%.
The extensive flow sheet development test work program outcomes were combined with operating performance data and working knowledge from the historical operations to develop a robust process plant flow sheet.
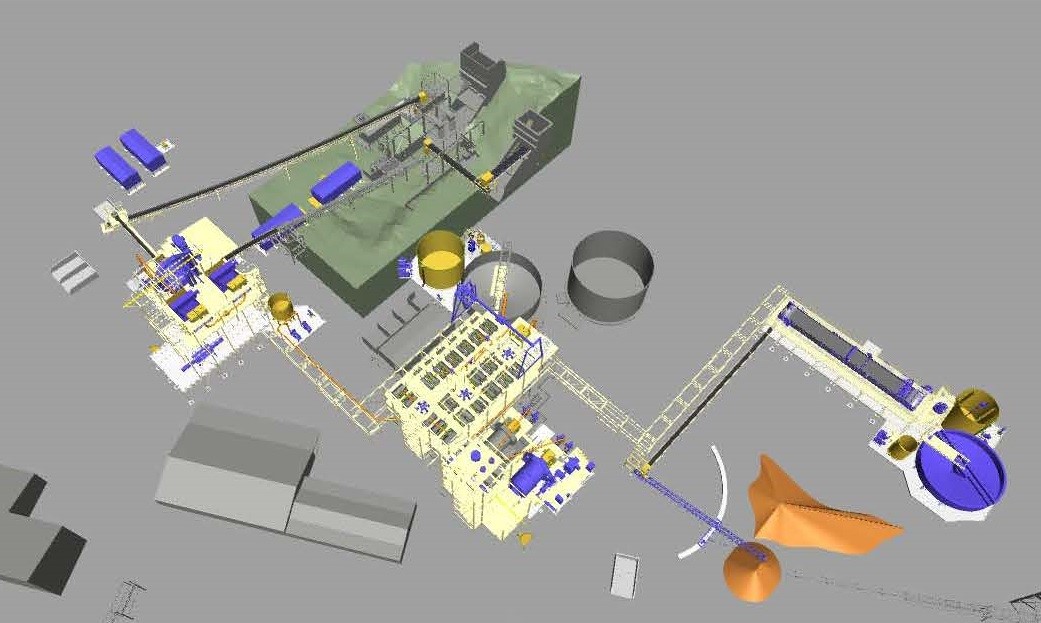
Crushing, Milling and Beneficiation (CMB) Overall Plant View
The new process plant flow sheet significantly simplifies operations at Windimurra compared to the existing plant and leverages the performance and learnings from the Xstrata operating design from 1999 to 2003.
Other significant changes identified in the DFS include production de-bottlenecking activities around the roasting kiln and associated infrastructure and the production of high-purity V2O5 flake rather than ferrovanadium. These changes will add significantly to the operability and overall technical success of the project.
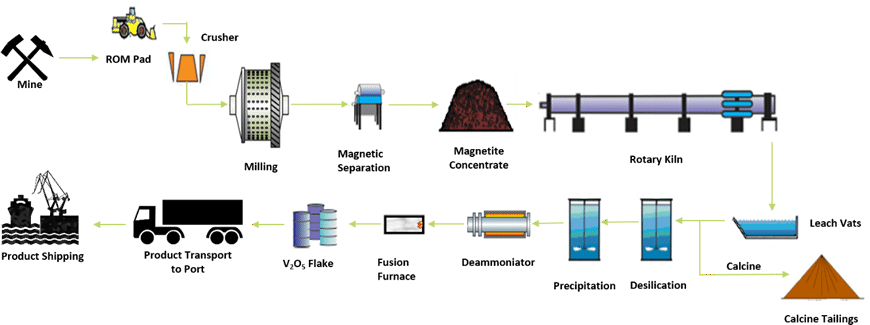
Windimurra Process Flow Diagram
Capital Costs
The capital cost of A$213 million for the development of the project was estimated to a -5% / +15% level by AVPL’s engineering contractor.